作者| 甘亚平,汽车行业高级工程师
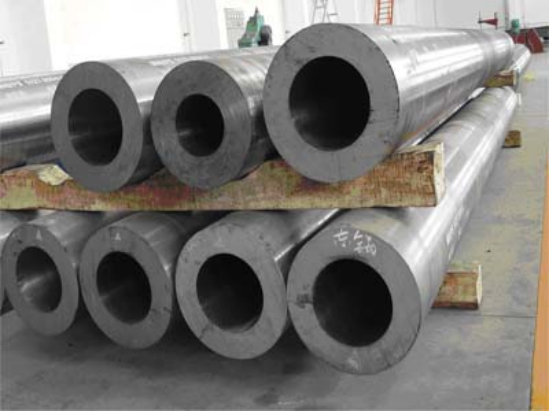
看到上面这幅图中的钢管,可能很多人会感到陌生,不过,我们日常使用的一种重要能源——电能,可是跟它有着非常密切的关系。
我们都知道,中国目前主要的电力来源是火电,而当前世界上火力发电站的发展趋势是建设60万千瓦以上超临界、超超临界发电机组,中国自然也不例外,这一切都离不开图片中的这种钢管——耐高温高压的厚壁特种钢管。
要制造这种钢管,就要用到一种特殊的装备:大型垂直金属挤压机。
(一)什么是金属垂直挤压机?
钢制品的生产方式通常有轧制、锻造、拉拔、挤压等,其中挤压是通过施加强大机械压力使被加工钢坯产生变形从模孔中挤出规定尺寸、形状成品的过程。而我们文章开头提到的垂直金属挤压机,就是用来挤压金属的大型设备。
垂直挤压工艺以铸造的钢锭为原材料,钢锭经加热,去除氧化皮后首先在镦粗穿孔制坯机上面进行坯料的闭式镦粗,穿孔制取管坯,然后空心管坯经过二次加热后,送入垂直挤压机进行挤压成型获得管材或者其他型材。
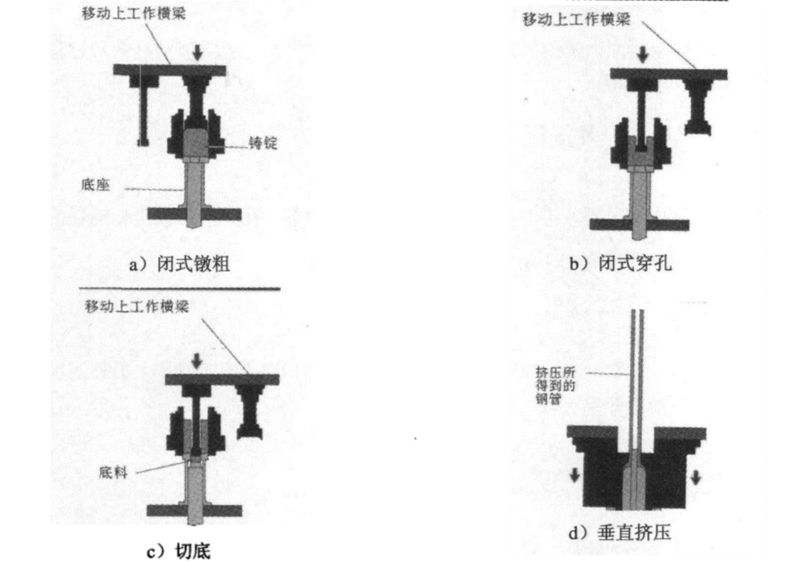
(钢管挤压原理图。挤压之前需要在穿孔制坯机上完成坯料镦粗穿孔工序,二次加热后由垂直挤压机挤压成最终产品)
在工业生产中,铁合金是用得最多的黑色金属,不过制造特种厚壁钢管要满足高温高压的使用环境,所以必须使用添加了大量钴,镍,锰,钒等合金元素的高合金钢材料。
高合金成分的引入使得本来就不好的流动性变得更差,软化温度更高,超过1100摄氏度,技术难度比有色金属铝,铜等材料的挤压要高得多,因此对挤压机的吨位、模具材料、模具设计、高温润滑剂等选用都是不小的挑战。
(二)垂直挤压机制造的厚壁无缝钢管,用处多多
文章开头我们已经提到,金属垂直挤压机制造的特殊厚壁无缝钢管是火力发电站中非常重要的材料。
其实不光火电站要用到这种钢管,核电站同样如此,而发电站要提高能源利用率,总是伴随着高温高压的极端工作状态。目前世界上发电机机组的主蒸汽压力为25~31MPa,主蒸汽和再热蒸汽温度为580~610℃。规划中的下一代汽轮机发电机组的蒸汽温度甚至接近700℃,压力接近35MPa。
没有建成大型垂直挤压机之前,大口径厚壁无缝钢管在中国传统的制造工艺是先将钢材锻造成棒料后钻孔加工。这种工艺材料浪费大,加工效率低,加工成本非常高,没有竞争优势。
而且,由于锻造过程中棒料芯部不容易压透,造成钢管机械性能受限,只能用在中小型汽轮机组上面,并不能满足超超临界机组的使用要求。
超超临界发电机组必须使用厚壁挤出无缝钢管才能满足更高的耐高温高压的使用要求。
无缝钢管的另一个使用大户是石油化工行业和煤化工行业。100万吨级乙烯装置、大型炼油装置、大型煤制油装置都需要高温高压的反应环境才能提高反应速率和产率。这些大型装置的管道同样需要大口径厚壁无缝钢管,中国重化工行业的飞速发展面临供应瓶颈。
(三)3.6万吨垂直挤压机打破美德日垄断
万吨以上黑色金属垂直挤压机,主要用于大型电站、石油化工行业急需的大口径厚壁无缝钢管制造,属于世界先进制造技术的极端领域,是一个国家制造能力的标志。
此前,世界上最大的垂直挤压机是美国威曼·高登公司花费7年时间研制的3.15万吨挤压机组,加上德国曼内斯曼公司、日本住友公司,这三家公司几乎垄断了世界全部耐高温高压厚壁成型材料。
由于国外长期技术封锁,中国高性能大口径厚壁无缝钢管不得不从国外大量高价进口,每吨钢管要价2万美金,不仅如此,购买还需要面临各种审查,采购周期非常长,基本上不可控。
而中国发电设备制造每年需此类钢管约10多万吨。进口材料使电站的建设成本始终降不下来,限制了中国核电、火电的发展。
既然直接买钢管价格高昂又手续繁琐,那么有没有可能跟国外公司合作呢?大型垂直挤压机具有显著的战略意义,而且还能够挤压航空发动机的高温合金涡轮盘,具有军用潜力,合作在中国建厂的道路被美国的出口管制法规堵死。而在德国,由于对方开出了高达1亿欧元的设计费,合作计划也宣告终止。
为打破国外高端材料的垄断,中国在充分调研论证的基础上启动研动36000吨黑色金属垂直挤压机项目。
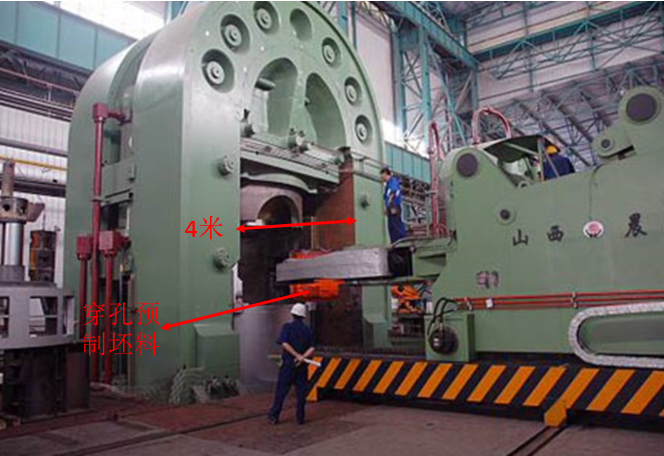
(黑色金属垂直挤压机之王,3.6万吨黑色金属垂直挤压机。大家可以根据参考尺寸想象一下整机的大小,妥妥的大国重器。)
3.6万吨垂直挤压机项目包括1台垂直挤压机及一台1.5万吨穿孔制坯机和相关辅助设备63台套的热挤压生产线项目,共历时3年,突破了很多制造及工艺难题,最终获得成功。
(四)“垂直挤压机之王”有何过人之处?
3.6万吨垂直挤压机是目前世界上最大最先进的黑色金属垂直挤压机,吨位和主油缸工作行程都优于美国威曼·高登公司的3.15万吨压机。 除此之外,它还有很多过人之处。
1、使用预应力钢丝缠绕结构,整机重量由14000吨缩减到4000吨
3.6万吨垂直挤压机使用了清华大学开发的预应力钢丝缠绕结构,在挤压机结构牌坊、挤压筒和液压油缸上都使用了这种结构,整机重量不足4000吨,传统结构的同等吨位垂直挤压机重量则接近1.4万吨。
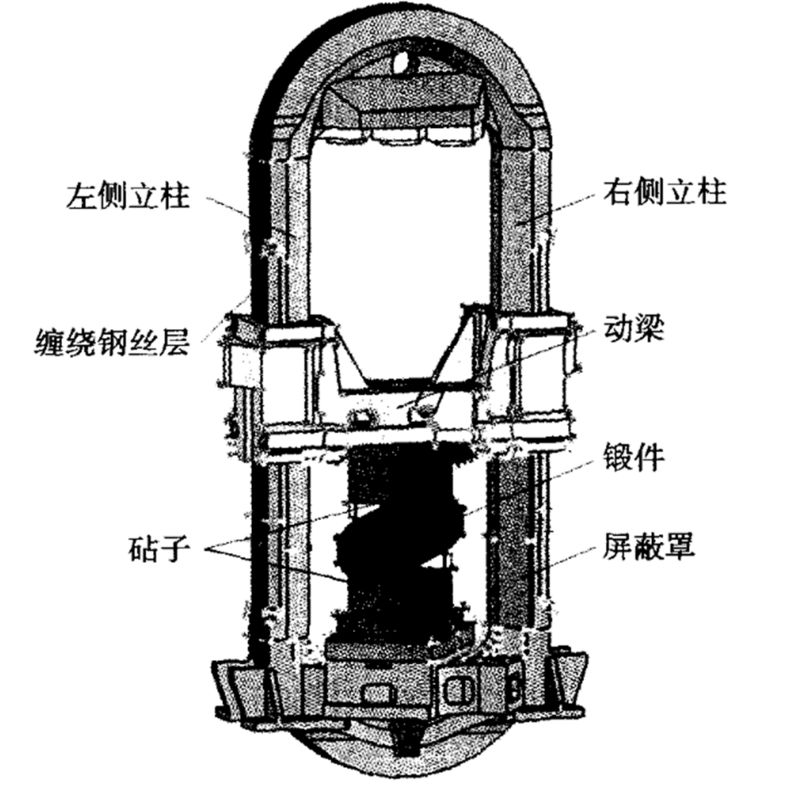
(清华大学开发的2000吨快速锻压机结构示意图。可以看到主结构牌坊外面缠绕的钢丝预应力增强层。3.6万吨垂直挤压机主结构牌坊的钢丝缠绕预应力增强层和这个非常类似,一母同胞。)
大型锻压机的结构一般采用铸钢铸造后加工,一般铸钢的许用强度不超过300MPa,而钢丝的许用强度可以轻松超过800MPa。使用高强度钢丝缠绕,工作时的载荷可以由钢丝缠绕结构承担,可以大幅降低结构重量,降低制造难度和成本,同时也降低了运输和安装的难度和成本。
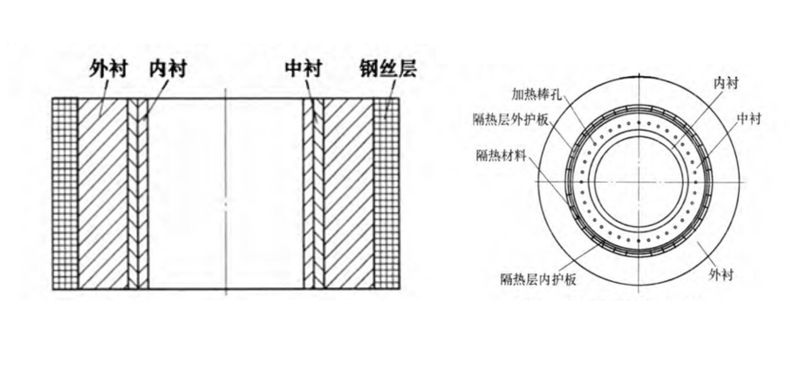
为了降低结构重量,保证挤压过程的稳定,研制团队在挤压套上面也是下足了功夫,采用了复合结构。
内衬由于要承受坯料的高温和挤压过程中金属流动的摩擦,采用耐高温的热作模具钢材料。
为了改善挤压过程中温度场的稳定,整机增加了一个带加热装置的中衬层,使得预加热后的坯料进入挤压筒后能够维持温度稳定,不至于散热冷却而降低材料的流动性。
外衬使用铸钢材料,中衬和外衬之间增加石棉隔热层,既能保温,又防止最外层钢丝缠绕增强层温度上升而导致许用强度下降。
2、使用预应力剖分坎合结构,降低了加工制造难度和成本
钢丝缠绕预应力结构可分为组合结构和坎合结构,对比见下表:
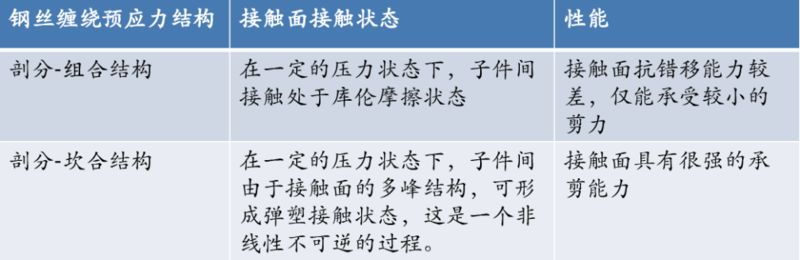
坎合结构可以保证更强的承载剪切载荷的能力,在满足设计强度的前提下,挤出机的主结构可以分成更小的子零件制造,再组合起来进行钢丝预应力缠绕。
子零件变小了,制造、运输、安装等全部过程都变得更容易,成本更低。
3、使用玻璃做润滑剂,降低摩擦力的同时还能形成保护层防止氧化
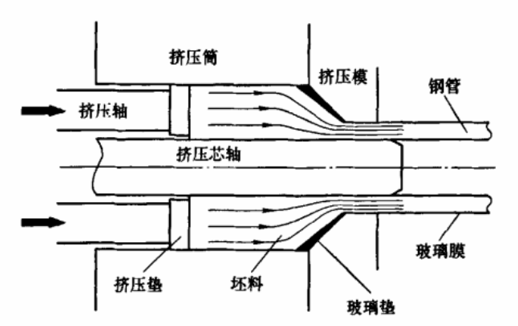
(钢管挤压原理图)
有色金属,比如铝合金和铜合金由于高温流动性非常好,挤压过程一般不需要润滑剂。而钢铁本身流动性就不好,在加上添加的难熔合金元素,这对于流动性更是雪上加霜,因此对于黑色金属的高温挤压来说,润滑剂的使用是工艺能否成功实施的核心要素之一。
一般的钢铁锻造工艺由于只是一个很短的过程,使用矿物油混合石墨就可以满足润滑的要求,但厚壁无缝特殊钢管的挤压过程是一个很长的过程,矿物油会在高温下挥发燃烧,石墨长时间的高温也会被氧化,因此不能作为钢管挤压的润滑剂使用,这时候需要使用玻璃润滑剂。
挤压过程中,将玻璃垫置于挤压模具前端,高温坯料(1150~1250摄氏度)会使玻璃垫软化,熔融,在挤压轴的作用下,随着流动的金属而流出,在坯料和模具之间形成20~40微米左右的玻璃膜,起到润滑和隔热作用。
而且,玻璃膜附着在钢管上面,还能防止高温的钢管和空气接触氧化,提高了钢管的表面质量,一举两得。而当钢管冷却的时候,由于玻璃和钢的膨胀系数不同,再加上玻璃本身是脆性材料,玻璃润滑保护层会自动破碎剥落,省掉了去除的麻烦。
玻璃润滑剂的使用能够大幅降低挤出过程中的摩擦力,降低模具的磨损,提高挤出零件的表面质量。同时,由于挤出过程中摩擦消耗占挤出力的30%以上,玻璃润滑剂的使用能够大幅降低能耗。
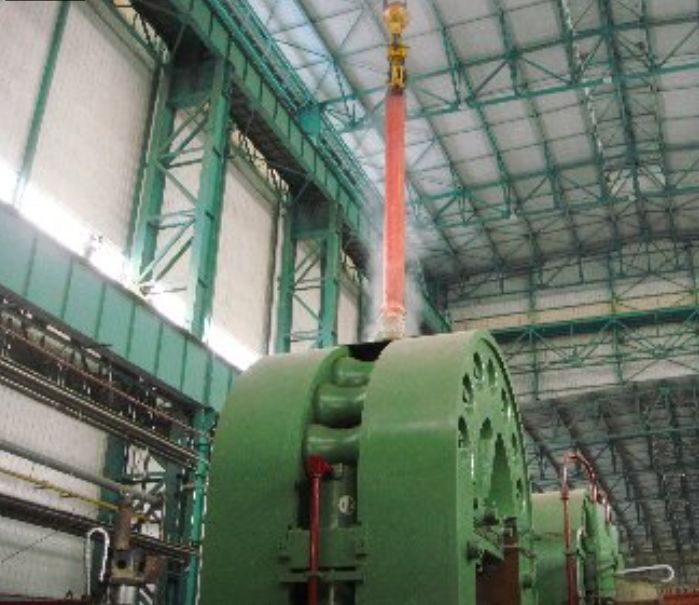
(3.6万吨垂直挤压机将穿孔预制坯料挤压出一根根直径1.3米,壁厚300mm的大口径无缝钢管)
4、使用新一代的高压直驱泵控系统,易用又节能
此前,在万吨级铝挤出机上,中国首次用到30Mpa压力的液压系统,首次使用变量泵和伺服阀。调速依靠变量泵流量控制,油缸换向依靠阀门换向。
而3.6万吨黑色金属垂直挤压机使用的是42MPa的双向变量泵直驱液压系统,完全取消了阀。液压缸的调速依靠变量泵的流量控制,液压缸换向则直接依靠双向变量泵直接换向,完全杜绝了阀门的节流损失和压力损失,而且系统简单,使用维护方便。
对于大型液压系统来说,泵直接传动和直接泵控已成为发展趋势,对于系统的节能降耗有着巨大的意义。
结语
中国截止目前百万千瓦级超超临界火力发电机组建设已经超过100座,大型化工项目,煤制油项目和沿海核电项目密集上马, 仅厚壁无缝钢管一项,每年就能节省采购成本几十亿元人民币。3.6万吨黑色金属垂直挤压机建成投产,标志着中国重型金属加工设备取得突破性发展。